HUNTINGTON BEACH, Calif., July 23, 2025 - Srixon’s heritage as one of Japan’s top Golf brands brings with it a legacy of extraordinary attention to detail and craftsmanship in the Iron space. Feel is paramount for our Iron performance, and any new feature or technology introduced to Srixon Irons is always designed with feel in mind.
For our all-new generation of Srixon Irons—ZXi—we overhauled our forging process to pursue previously-unseen improvements to Iron feel. Collectively, we call this family of improvements: i-FORGED.
This paper provides a brief overview of i-FORGED’s development and it’s overal impact to feel and performance across the ZXi Iron lineup.
PLAYER-FOCUSED DESIGN
Through a series of consumer insight surveys1, feel performance clearly emerged as a main priority for Srixon players. Our two key findings were:
Firstly, that nearly 95% of those surveyed reported “feel” was at least “Very Important” in the Irons they play.
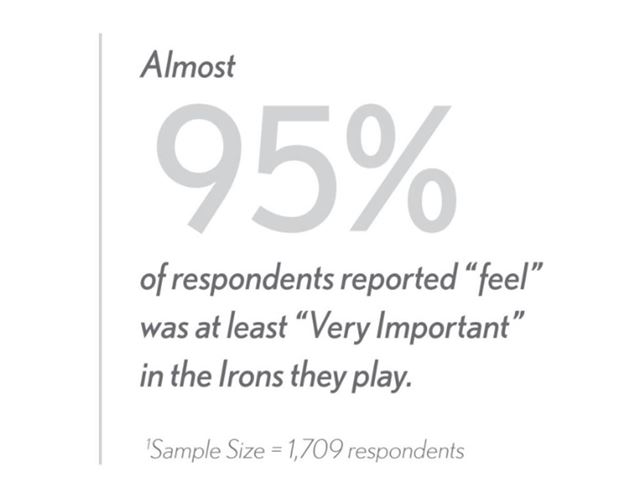
The degree to which respondents felt that “feel” was at least “Very important” in an Iron showed us that pursuing feel improvements aligned with player sentiments.
Further supporting our focus on Iron feel, respondents cited “feel” as the biggest reason they ultimately purchased Srixon Irons, and by a significant margin.
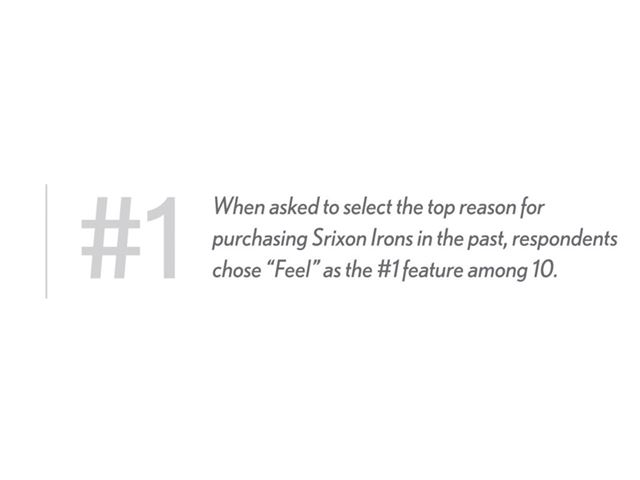
TO GO SOFTER, WE WENT STRONGER
Building upon decades of forging experience, we knew that one of the most direct ways to improve an Iron’s feel is to soften the club’s face or material. There are a number of ways to do this—including selecting a material with softer properties or adjusting the heat treatment of the finished product. However, there are tradeoffs when trying to soften golf clubs. The biggest one being durability.
Softer metals can quickly bend out of spec, even with normal use. An improperly bent Iron can create undesired loft and address angles, resulting in misshits. So, to make our Irons softer, we first needed to find a way to make up for any potential durability losses.
THE BENEFITS OF CONDENSED FORGING
To crack the code of how to implement new, softer materials and heat treatment processes without sacrificing durability, Srixon R&D teams in Japan and the U.S. first ran exhaustive simulations to determine which areas of an Iron head would be most susceptible to bending with the use of a softer material. In one-piece forged Irons, this was determined to be the Iron’s hosel. For multi-piece forged Irons, R&D found the topline and toe-side of the blade to be the most vulnerable. Those key areas needed fortification for us to implement softer materials.
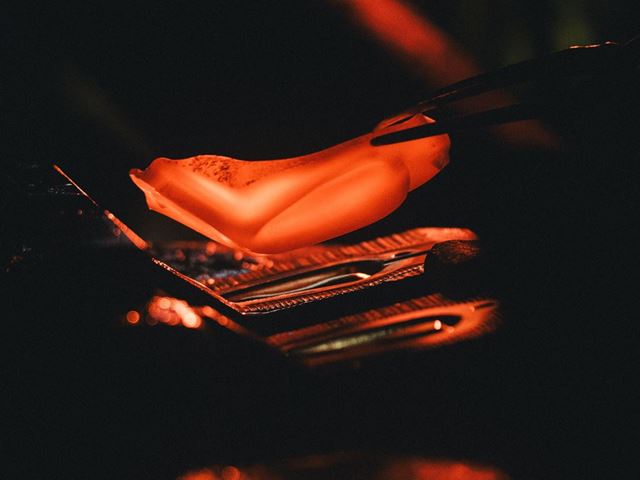
FIRST FORGE
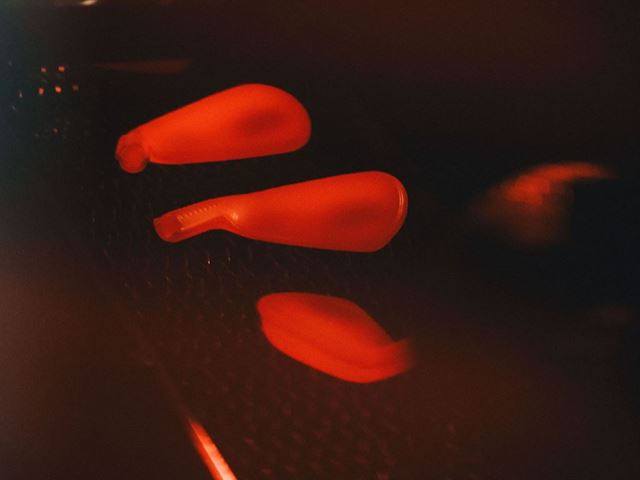
To solve this, we worked alongside our renowned Japanese forging partners to develop the main component of i-FORGED, called Condensed Forging. In short, the Condensed Forging process adds strength to targeted locations, allowing the rest of the iron body to be made from new, softer steel. It works by imprinting an array of raised protrusions into the steel during the Iron’s first forging step, then smashing those same protrusions back into the steel in a later forging step. Since we already knew from our simulations which areas were considered most vulnerable to bending over time, it became a matter of focusing this Condensed Forging technique on those areas.
REHEAT
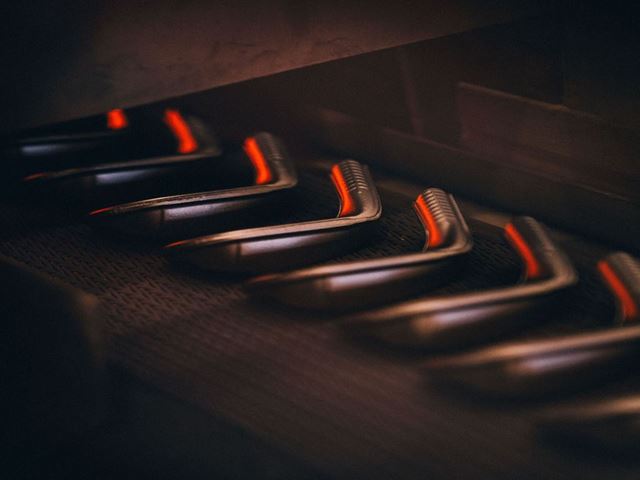
Condensed Forging starts during the first forging step, when raised ridges are pressed into the areas of the clubhead most in need of extra strengthening. After trimming and cooling, the Iron head is reheated with the raised elements being smashed smooth in the final forging step of the process.
FINAL FORGE
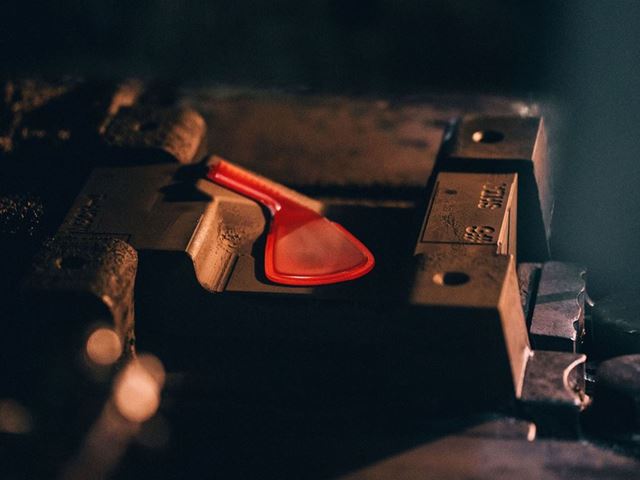
The end result strengthens the specific area of the club where the ridges are located. When we smash these ridges flat the metal’s structure changes at the microscopic level. This smashing increases strength by adding imperfections at the atomic level (referred to as “dislocations” in material science).
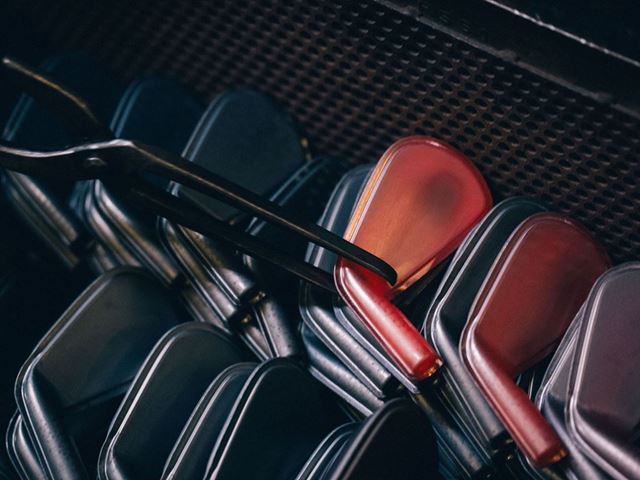
ZXi7 IRONS TECHNOLOGY
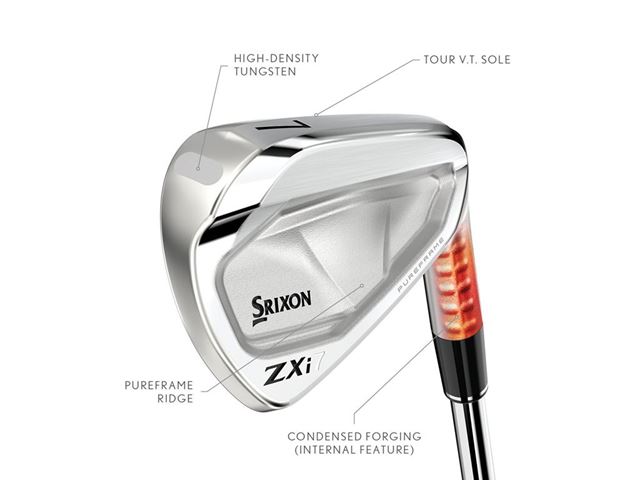
For ZXi7, our one-piece forged Iron, we applied Condensed Forging to the hosel. This strengthened hosel allowed us to use an exciting new material called S15C steel, measured to be 7%2 softer than our previously used steel. Coupled with other improvements, players should expect an Iron that delivers best in-class feel and feedback on every swing, which is especially important for high-skill golfers.
ZXi5 IRONS TECHNOLOGY
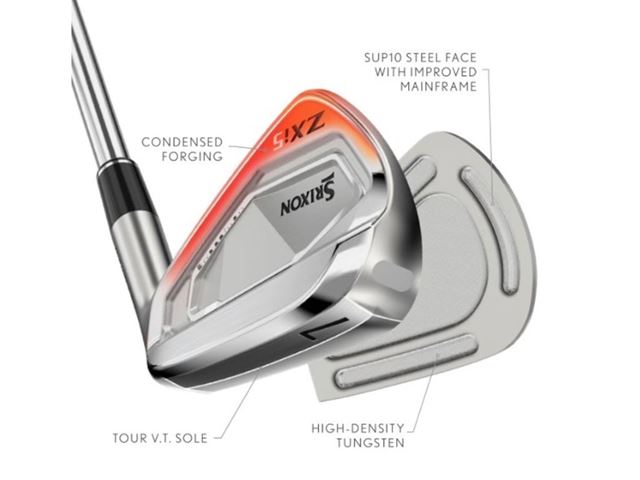
For ZXi5 and ZXiU, we kept the same materials from the last generation, as they fit the design goals of these models. However, we still sought to improve feel for this generation. Once again, Condensed Forging became the solution. In this case, our testing determined the topline and toe-side of the blade of the Irons needed enhanced strength. Condensed Forging in this area allowed Engineering to adjust the heat treatment on the Iron face plates, making them 14%2 softer than previous generations, without sacrificing durability.
2Calculations based on difference in material hardness between ZX Mk II and ZXi Irons using Vickers hardness scale.
i-FORGED in ZXi4
Based on comments from our fitting partners, we knew the ZXi4 line needed improved hosel bendability. A large range of players have uses for the added distance and forgiveness of a hollow-body Iron, so a softer hosel that was easily bendable (while still maintaining shape during play) was preferred to fit a larger player base with ZXi4.
We selected a new material for ZXi4 called SUS 17-47. This material had the necessary durability to stand up to a new heat treatment applied locally to the hosel, softening it by 30%3 over the previous generation, and allowing the hosel to bend more like our other ZXi series Irons. This new ZXi4 manufacturing change added bendability alongside improvements to MainFrame and other performance features, making ZXi4 an ideal choice for a wide range of golfers.
3Calculations based on difference in material hardness between ZX Mk II and ZXi Irons using Vickers hardness scale.
FINAL THOUGHTS
As Srixon continues to lead the push for the most responsive, best feeling Irons on the market, we look forward to i-FORGED’s reception by our player base.
We encourage all players to test our ZXi Irons in a store or fitting experience. We anticipate they will be at the top of your list for feel, control, and feedback—much of which can be attributed to the material changes made possible by Condensed Forging. When your Irons feel better, you will play better; and, ultimately, our goal is to inspire confidence and unlock the Iron game for players of all skill levels.